発注方式のモヤモヤを解消する(後編) ~教科書通りにはいかない!?様々な発注方式と、実務における考慮点~コラム
公開日:2022年9月15日
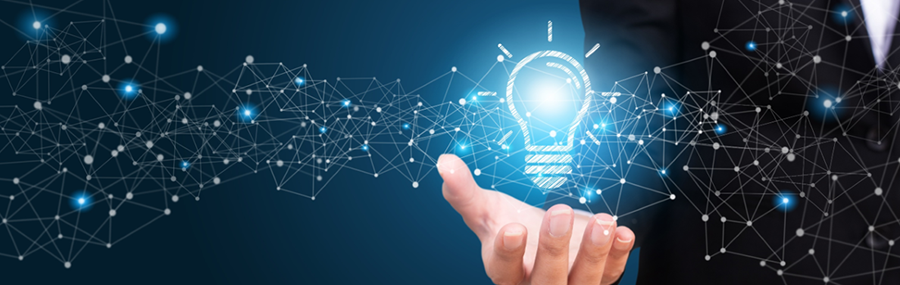
昨今、経済・社会環境は急激に変化し続けています。それによっておこる社会課題やトレンドに対し、需要予測・需給計画は柔軟に対応していく必要があります。
そこで本コラムでは、需要予測・需給業務の担当者や最新のトレンドを学びたい方向けに、今後必要とされる需要予測・需給計画の取り組みやポイントについて、弊社コンサルタント独自の視点で解説します。
発注方式のモヤモヤを解消する(後編)
前回は、発注方式の5つのモヤモヤポイントについてお話しました。今回はこれらのモヤモヤを1つずつ解消していきたいと思います。
需要が一定という前提がありえない
実務において需要が一定というケースはほとんどありません。需要予測に基づいて発注することが必要となります。例えば発注点方式の場合は発注点を次の式で動的に求めることで需要の変動に対応することができます。
発注点=調達期間内の需要予測+安全在庫 (4)
定期発注方式の場合は発注量を次の式で求めます。
発注量=(発注間隔+調達期間)内の需要予測+安全在庫-現在の在庫量-現在の発注残 (5)
時間の概念が連続的となっていて現実的ではない
実務においては在庫数の把握や発注・納品といった業務は日単位で行われていることが多く(時間単位や月単位など業種・業態によって異なります)、連続時間で考えるのは現実的ではありません。ここでは1日1回、前日末在庫を把握し、調達期間や発注間隔は日単位で設定されており、入庫した商品はその日の内に販売可能とします(この前提もケースによって異なります)。この前提では、定量発注方式の発注点の式(4)は以下のように修正が必要となります。
発注点=(1+調達期間)内の需要予測+安全在庫 (4’)
前日在庫を前提としているので、発注日当日の使用量も考慮する必要があるからです。一方、定期発注方式の発注量は修正の必要はありません。発注間隔の中に当日を含んでいるからです。
365日いつでも発注できる、一定間隔で発注する、などは現実的ではない
いつ発注可能かは、以下2つの要素で決まります。
① 発注者がいつ発注可能か?
発注者が発注業務をどのタイミングで実施可能かによって発注タイミングは制約されます。休みなしで働かなければ毎日発注はできませんし、たとえ休みがなくても週に1日しか発注業務に時間が割けなければ週1回発注ということになります。
② 発注先がいつ対応可能か?
発注先の都合によっても発注タイミングは制約されます。発注先が休みのときは発注を受け付けてもらえませんし、翌月の生産計画の確定時期が毎月20日の場合、それを過ぎれば原則翌々月生産になりますので実質月1回発注となります。
このように、完全な毎日発注も定期発注も実際には存在せず、常に不定期発注と考えておくべきです。この前提で考えると、発注点は次の式で表すことができます。
発注点=実効リードタイム期間の需要予測+安全在庫 (6)
実効リードタイム=次回発注までの間隔+調達期間 (7)
ここで実効リードタイムとは、次回発注の入庫日前日までの期間を表しています。毎日発注の場合、次回発注までの間隔は1日ですので、
発注点=(1+調達期間)内の需要予測+安全在庫 (6’)
となり、式(4‘)と一致していることが分かります。また、発注量は次の計算式で求めることができます。
発注量=実効リードタイム期間の需要予測+安全在庫-現在の在庫量-現在の発注残 (8)
次回発注の入庫日前日までの需要をカバーするように発注すればよいということです。式(6)(8)をよく見ると式(8)は次のように書き換えることができます。
発注量=発注点-現在の在庫量-現在の発注残 (8’)
自由に発注量を決められるとは限らない
式(8’)の発注量は発注する側の都合だけで決めた必要最低限の発注量です。しかし、発注先からすると生産や輸送の都合で受け入れられない場合があります。そのため実務では最低発注量や発注ロット(この倍数で発注しないといけない)を指定されるケースがほとんどです。したがって式(8’)は次のような修正が必要です。
発注量=(発注点-現在の在庫量-現在の発注残)のロット丸め後数量 (9)
定期か定量かという視点だけで発注方式がネーミングされていて本質を表していない
以上のことから2つの計算式を得ることができました。
発注点=実効リードタイム期間の需要予測+安全在庫 (6)
発注量=(発注点-現在の在庫量-現在の発注残)のロット丸め後数量 (9)
実は、この2つの式で定量発注方式も定期発注方式も表現できています。
定量発注方式の発注点が式(6)で表現できることは既に示した通りですが、発注量は式(9)によると非常に小さな数量(発注間隔1の定期発注とみなせるので1日分の需要量を発注すればよい)になります。実際は経済的発注量や発注先の制約によって丸められるので、結果として大きな発注量になるというだけです。
一方、定期発注方式の場合、発注量が式(9)で表現できることは既に示した通りです。この発注量は発注点をギリギリ満たす量なので、よほど需要の変化がない限り次回発注のタイミングで在庫が発注点を上回ることはありません。つまり毎回発注が必要(定期発注)となります。
このように式(6)(9)と発注可能日、調達期間の情報を組み合わせることでほとんどのケースに対応することができると考えています。皆さん、モヤモヤは解消されたでしょうか?ただ、この発注方式の良いネーミングが思いつきません。やっぱりモヤモヤします。
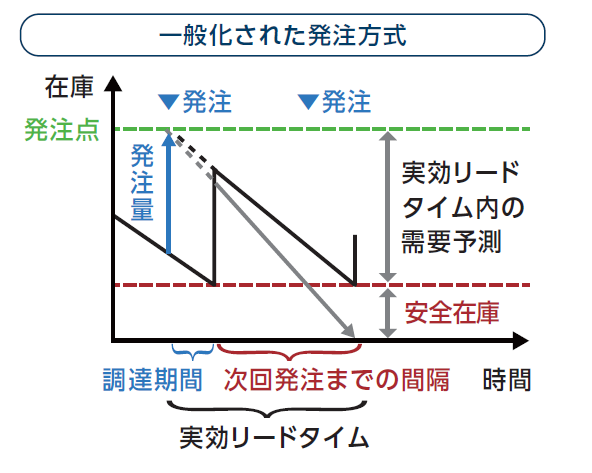
筆者紹介
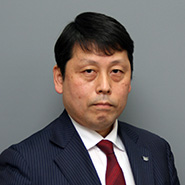
淺田 克暢(あさだ かつのぶ)キヤノンITソリューションズ株式会社 R&D本部 数理技術部 コンサルティングプロフェッショナル。
「需給マネジメント」の普及を目指し、20年以上に渡って需給計画システムの導入コンサルティング業務に従事。中小企業診断士、流通科学大学非常勤講師(2003~2006年)、現在は東京理科大学のSCM関連の講義を担当。著書に『在庫管理のための需要予測入門』(共著、東洋経済新報社)、『なぜあなたの会社はITで儲からないのか』(共著、同友館)。
関連書籍など
在庫管理のための需要予測入門
FOREMAST担当コンサルタントが執筆した需要予測入門書です。
どのような需要予測システムを導入すればよいかお悩みの方のために、実務に精通したコンサルタントが基本知識からシステム導入時に考慮すべきポイントまでをやさしく解説しています。
在庫管理のための需要予測入門
キヤノンシステムソリューションズ株式会社数理技術部[編]
淺田 克暢+岩崎 哲也+青山 行宏[著]
- 出版社:東洋経済新報社
- 発売日:2004年12月22日
- ISBN:4492531874
- 価格(税込):1,980円
関連するソリューション・製品
- FOREMAST
- 大量の在庫を抱えているのに欠品や納期遅れが発生していませんか?「キャッシュフロー経営」が叫ばれる中、多くの企業で在庫削減が重要な経営課題となってきています。しかし一方で、お客さまからの即納・短納期要求は益々強くなってきており、欠品の発生が企業経営に大きな影響を与えるケースも増えてきました。FOREMASTは、科学的な需要予測に基づく在庫補充計画と、需給計画・実績情報の共有支援、問題の見える化により、欠品なき在庫削減の実現を支援します。